Exploring the World of Prefab Building
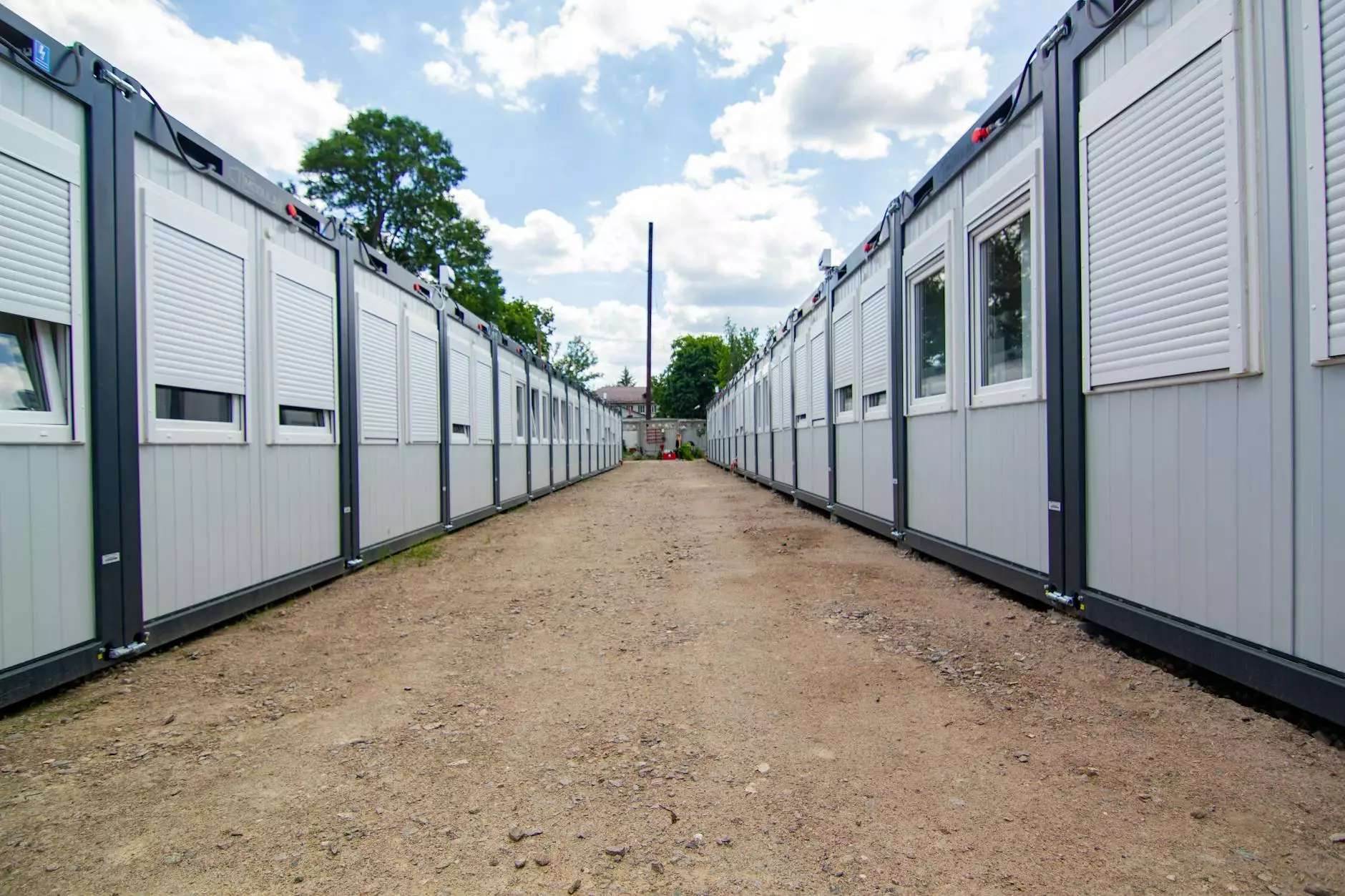
In today's fast-paced world, the construction industry is experiencing a significant transformation, largely driven by innovative practices and sustainability efforts. Among these advancements, prefab building has emerged as a game-changer. This article delves deep into the concept of prefab construction, its benefits, applications, and why it is the future of the building industry.
What is Prefab Building?
Prefab building, or prefabricated construction, refers to structures that are manufactured off-site in a factory setting and then transported to the building site for assembly. This method contrasts with traditional building methods, where construction occurs solely on-site.
The parts of a prefab building are produced in a controlled environment, allowing for higher precision, quality, and reduced waste. From single-family homes to large commercial buildings, prefabrication can be applied to a variety of construction projects.
The Benefits of Prefab Building
There are numerous advantages of adopting prefab building techniques, making it a compelling choice for contractors and clients alike. Here are some of the key benefits:
- Cost Efficiency: Prefab buildings reduce labor costs and material wastage, leading to substantial savings on construction projects.
- Time Savings: With parts fabricated simultaneously while site preparation is underway, the entire construction timeline is significantly shortened.
- Enhanced Quality Control: Factory settings enable stricter quality assurance processes, resulting in higher quality structures that meet industry standards.
- Sustainability: Prefabrication minimizes waste through efficient manufacturing processes and often uses sustainable materials, reducing the environmental impact.
- Design Flexibility: Various designs and layouts can be created to meet specific needs, from residential homes to commercial spaces.
How Does Prefabrication Work?
The process of prefab building typically involves several stages:
- Design Phase: Affluent architects and designers create schematics based on client requirements and local building codes.
- Manufacturing Phase: Materials are sourced, and components are manufactured in a controlled factory environment, ensuring quality control.
- Transportation Phase: Completed components are transported to the construction site, ready for assembly.
- Assembly Phase: Skilled contractors assemble the prefabricated components into a finished structure.
Applications of Prefab Buildings
The versatility of prefab building allows for its application across various sectors:
Residential Construction
Many homeowners are opting for prefab homes due to their affordability and quick occupancy times. These homes can be customized to suit personal aesthetics and functional needs, offering a cost-effective solution without compromising quality.
Commercial Buildings
As businesses strive for quick and efficient building solutions, prefab commercial structures, such as offices, schools, and retail spaces, have gained immense popularity. These structures can be designed to meet specific business needs while ensuring adherence to local regulations.
Industrial Facilities
Many manufacturers are now utilizing prefab methods for industrial plants and warehouses. The reduced construction time allows businesses to start operations sooner, which is crucial in a competitive market.
Challenges and Considerations in Prefab Building
While the benefits of prefab building are numerous, there are also challenges that must be addressed to ensure successful implementation:
- Initial Costs: Though overall costs may be lower, the initial investment in design and manufacturing can be substantial.
- Regulatory Hurdles: Different jurisdictions may have specific regulations that impact the use of prefabricated structures, which can complicate the approval process.
- Perception Issues: Some clients may still associate prefab buildings with a lack of quality or durability, requiring education and reassurance from contractors.
Choosing the Right Contractor for Prefab Building
Selecting the right contractor is crucial for the successful execution of a prefab building project. Here are some tips for choosing the ideal partner:
- Experience with Prefabrication: Look for contractors with a proven track record in prefab construction.
- Portfolio of Work: Review their past projects to gauge quality and style compatibility.
- Client Testimonials: Seek feedback from previous clients for insights into their work ethic and reliability.
- Customization Capabilities: Ensure the contractor has the ability to customize according to your specific needs.
The Future of Prefab Building
As technology advances, the future of prefab building looks promising. Innovations such as 3D printing and enhanced modular construction techniques are set to further streamline the prefab process.
Moreover, as sustainability and efficiency continue to be prioritized in construction, prefab methods are likely to play a central role in meeting the demands of green building initiatives. The shift towards eco-friendly construction practices means that more contractors and clients will consider prefab building as a viable path forward, resulting in a transformative effect on the industry.
Conclusion
The world of construction is evolving, and prefab building serves as a key component in this transformation. With its myriad of benefits, diverse applications, and growing acceptance, it is surpassing traditional construction methods in many areas. Whether for residential or commercial purposes, embracing prefab building can lead to significant advantages in terms of cost, time, and quality. As more companies like Module T harness the power of prefabrication, the future of the construction industry promises exciting developments that will undoubtedly improve the way we build.