Unlocking Success in Business through Expert PLC Maintenance and Electronic Distribution
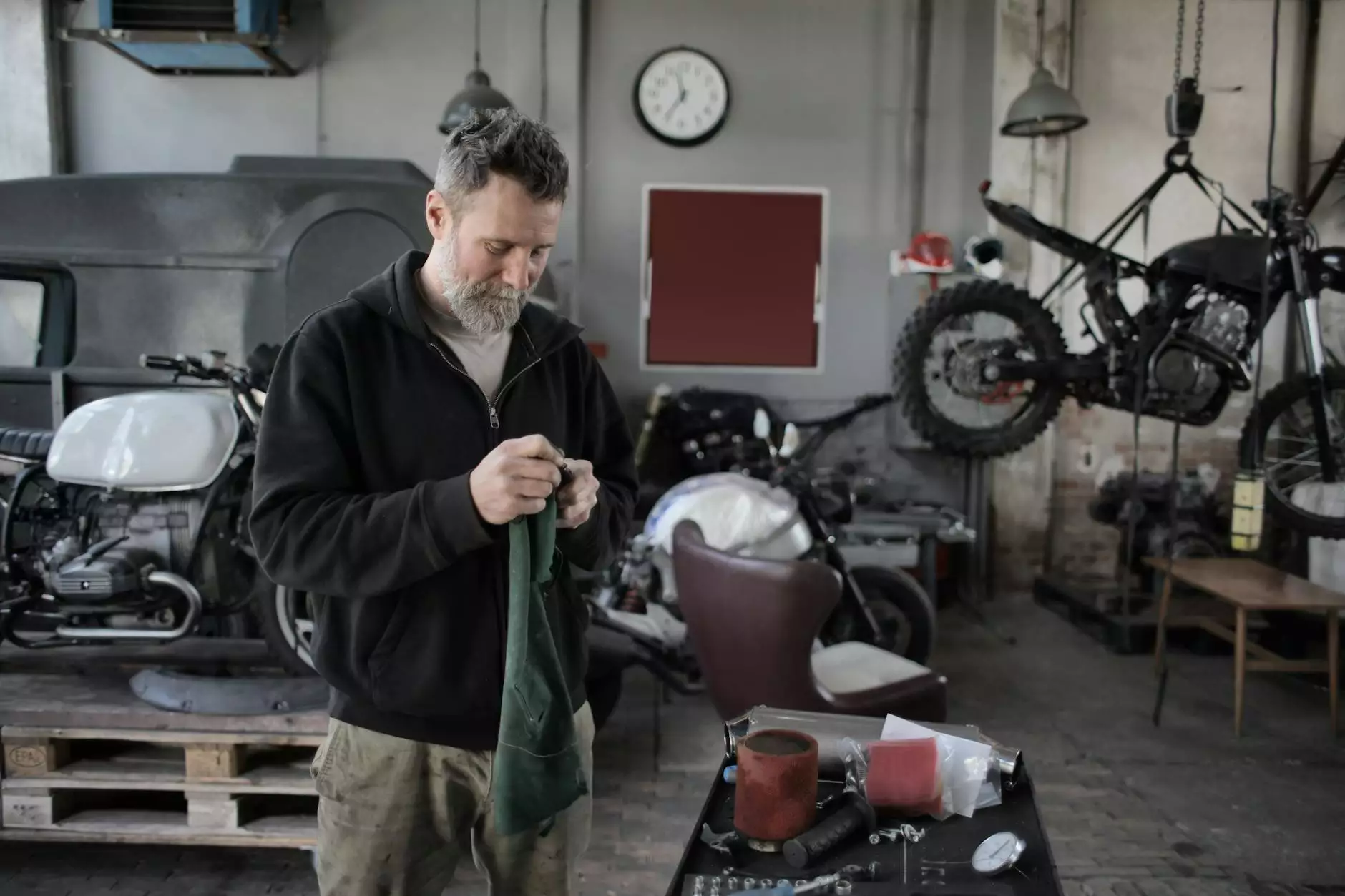
In today’s rapidly evolving industrial landscape, staying ahead in business requires a thorough understanding of both operational excellence and technological advancement. One of the cornerstones of this evolution is the importance of PlC maintenance and reliable access to quality electronic components. This article explores the intricacies of PLC maintenance, its significance, and how partnering with a top-tier electronic components distributor like QF Automation in Canada can catalyze your business growth.
The Role of PLC in Modern Industries
The Programmable Logic Controller (PLC) has revolutionized the way industries operate. These durable digital computers control manufacturing processes, machinery, and other automated tasks. Before we delve into PLC maintenance, it is crucial to understand the pivotal role PLCs play in industrial automation:
- Real-time control: PLCs ensure operations run smoothly in real-time.
- Increased efficiency: Automation reduces manual errors and increases throughput.
- Flexibility: PLC systems can be easily adapted to changing processes.
- Data monitoring: Collects data to improve operations and troubleshoot issues.
What is PLC Maintenance?
PLC maintenance encompasses routine checks, troubleshooting, repairs, and updates to ensure that your PLC systems function optimally. The importance of PLC maintenance cannot be overstated, as it directly impacts the efficiency, safety, and profitability of industrial operations.
Importance of PLC Maintenance
1. Minimizing Downtime: Regular PLC maintenance helps identify potential issues before they escalate into major failures, which can result in costly downtime.
2. Extending Equipment Lifespan: Just like any other piece of technology, PLCs require regular upkeep to extend their lifespan and ensure they operate at peak efficiency.
3. Ensuring Safety: Faulty PLC systems can lead to dangerous situations. Regular maintenance ensures all safety protocols are met, creating a safer working environment.
4. Cost Efficiency: Maintaining your PLC can save significant costs over time by preventing major repairs due to neglect.
Key Components of Effective PLC Maintenance
Engaging in a systematic PLC maintenance routine involves various components, such as:
- Regular Software Updates: Keeping software updated to benefit from improvements and bug fixes.
- Routine Inspections: Full inspection schedules to check connections, wiring, and physical components.
- Calibrations: Ensuring sensors and instruments are correctly calibrated to maintain accuracy.
- Documentation: Keeping detailed records of maintenance work helps troubleshoot future issues.
The Benefits of Partnering with an Electronic Components Distributor
Choosing to work with an experienced electronic components distributor like QF Automation offers numerous advantages, particularly in the realm of maintaining and upgrading your PLC systems.
Access to Quality Components
A significant advantage of utilizing a distributor is the access to a wide range of quality components. QF Automation specializes in providing top-notch electronic components, ensuring that you have reliable supplies when conducting PLC maintenance. Some of the benefits include:
- Variety of Products: A distributor offers a vast selection of components, accommodating specific needs.
- Quality Assurance: Products come with quality certifications that guarantee performance and reliability.
- Timely Supply: Having a dependable partner ensures fast delivery, which is crucial during emergency repairs.
Expert Consultation and Support
Another key benefit of working with an established distributor is the expert guidance they offer. With a comprehensive understanding of the industry and its demands, QF Automation provides:
- Expert Technical Support: Access to knowledgeable professionals who can help troubleshoot issues and recommend solutions.
- Training and Resources: Opportunities for staff training on new technologies and best practices.
- Industry Insights: Valuable information on emerging trends that can help your business stay competitive.
Best Practices for PLC Maintenance
To maximize the benefits of your PLC maintenance, adhere to the following best practices:
Implement a Maintenance Schedule
Establishing a routine maintenance schedule helps ensure no aspect of your PLC system is overlooked. This schedule should detail:
- Frequency of checks (daily, weekly, monthly).
- Specific maintenance tasks to be performed.
- Assigned personnel responsible for each task.
Train Your Staff
Investing in training for your team can greatly enhance your PLC maintenance efforts. Ensure that your staff is well-equipped with knowledge on:
- How to perform routine checks and basic troubleshooting.
- Understanding the PLC programming basics.
- Awareness of safety protocols when working with PLC systems.
Utilize Diagnostic Tools
Employing advanced diagnostic tools allows for more effective monitoring of your PLC systems. Tools such as:
- Diagnostic software that highlights potential issues.
- Sensor and signal monitoring devices for real-time data.
- Automated alerts for performance anomalies.
Conclusion: The Future of PLC Maintenance and Business Success
In conclusion, the importance of PLC maintenance cannot be underestimated in our technologically-driven industrial realm. Operational efficiency, safety, and overall productivity hinge on the reliability of these critical systems. Investing in a proficient electronic components distributor like QF Automation in Canada provides businesses with the essential resources and expertise needed to thrive.
By understanding the critical role of PLCs, establishing rigorous maintenance routines, and partnering with trusted suppliers, businesses can unlock significant potential for growth and innovation. With the right support, your PLC systems can function as robust backbones of your operations, enabling you to not only keep pace with industry demands but also lead your sector into the future.